What is a Digital Twin?
A digital twin is a technology that creates a digital replica of a physical entity, system, or process. This technology produces an exact equivalent of an object in the physical world within a digital environment, enabling monitoring, analysis, and optimization of that object. By leveraging advanced technologies like the Internet of Things (IoT), artificial intelligence (AI), and data analytics, digital twin technology facilitates the creation of digital twins for physical assets.
Imagine a coffee machine that has an exact digital counterpart in a virtual environment. This digital replica allows you to view the coffee machine’s unique details, such as its production location, model, etc. This replica is known as the digital twin of your coffee machine. With this digital twin, both users and manufacturers can monitor, analyze, and optimize the machine’s performance seamlessly.
Innovative solutions like those offered by sqanit go a step further, allowing users to access operating instructions simply by scanning a QR code—no need to download an app. They can quickly check the machine’s status through pre-set questions and answers that address common issues experienced by other users with similar machines. If more help is required, users can easily create a support ticket to report their issue, ensuring a smooth follow-up process.
Because the device’s information is already stored in the system via its digital twin, customer representatives can instantly identify the device and provide tailored solutions, without needing extra details from the users.
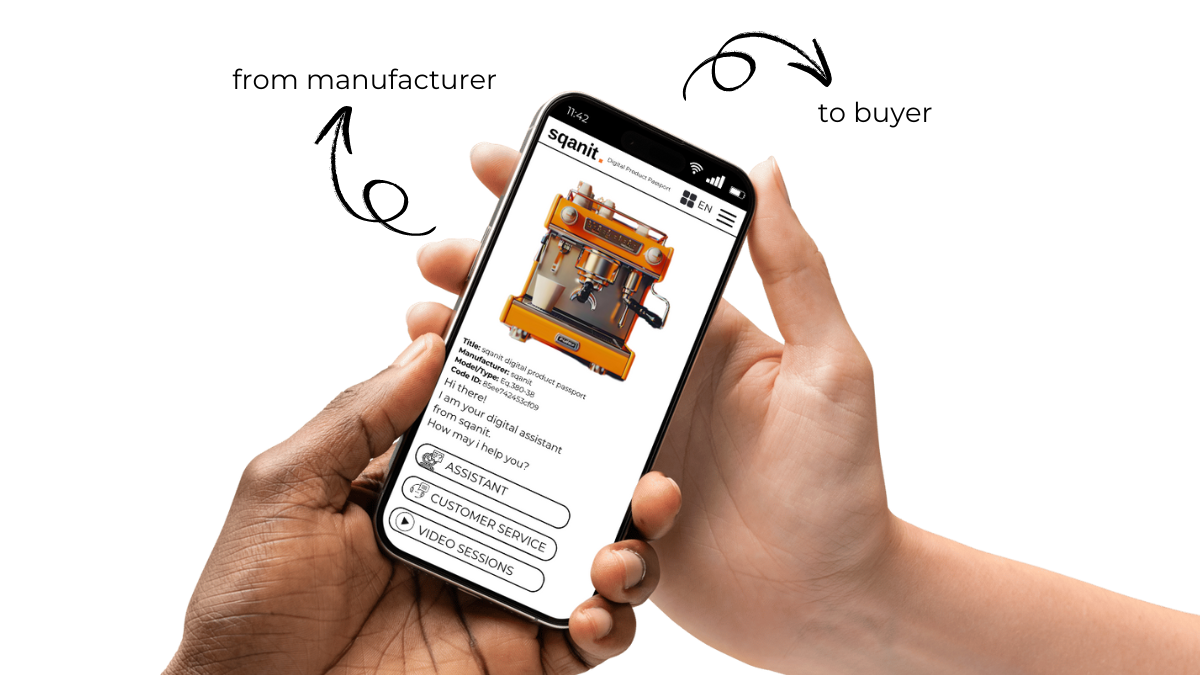
Additionally, for issues that can’t be resolved through support tickets, users can make video calls with customer service using Augmented Reality (AR) technology. This allows them to receive expert assistance remotely, making problem-solving more efficient.
Now, let’s explore these exciting advancements in more detail.
If you would like to learn more about Digital Twins, Digital Product Passports and explore the opportunities this innovative solution offers, please fill out this form, and we will get in touch with you.
How Does a Digital Twin Work?
Digital twins are generated using real-time data collected from a physical asset. This data is gathered through sensors, stored in a database, and processed within a digital model, ensuring a continuous flow of information between the physical asset and its digital counterpart. The process involves the following steps:
Feedback and Optimization: The insights gained from the twin’s analysis are utilized as feedback to optimize the performance of the physical asset, enhancing efficiency and effectiveness.
Data Collection: Sensors collect various data points from the physical object. For instance, a machine might provide information on temperature, vibration, or energy consumption.
Data Transfer: The collected data is transmitted to the digital twin via IoT infrastructure, facilitating seamless communication.
Analysis and Simulation: The twin analyzes the incoming data, assesses the performance of the physical asset, and runs simulations to predict future behavior.
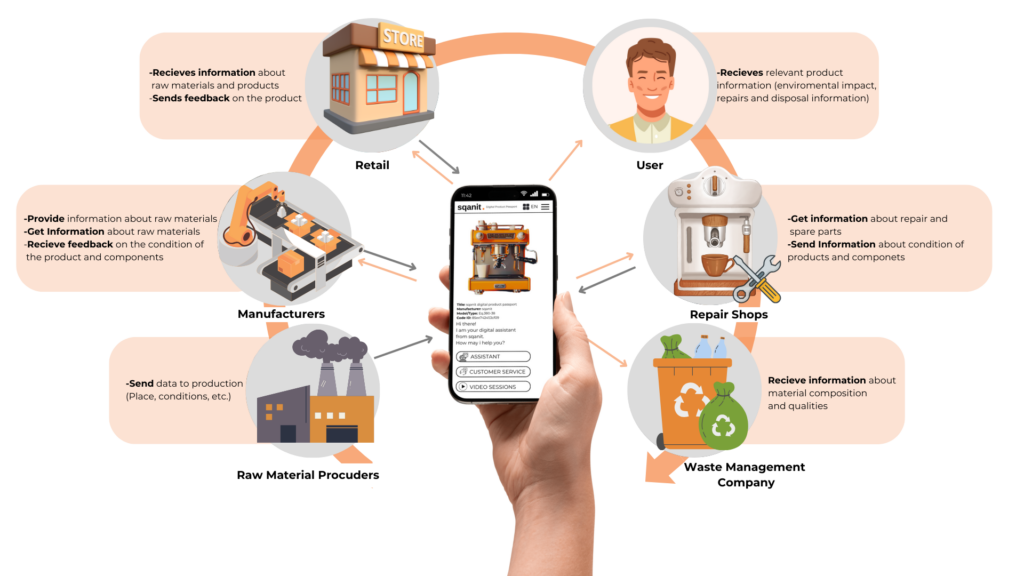
Advantages of Digital Twin Technology
Real-Time Monitoring: Digital twin technology allows for real-time monitoring of physical assets, enabling the immediate identification of issues and swift interventions, particularly in industrial processes.
Maintenance and Repair Management: By providing comprehensive information on the condition of machines and equipment, twins facilitate the development of proactive maintenance and repair strategies. This ultimately leads to reduced downtime and lower maintenance costs.
Simulation and Optimization: Twins can be utilized to test the design and functionality of new products or processes. Simulations conducted in a digital environment help identify the best design and operational methods before any physical prototypes are created.
Enhanced Efficiency: The data generated from digital twins contributes to optimizing production processes and operational efficiency, resulting in greater productivity at reduced costs.
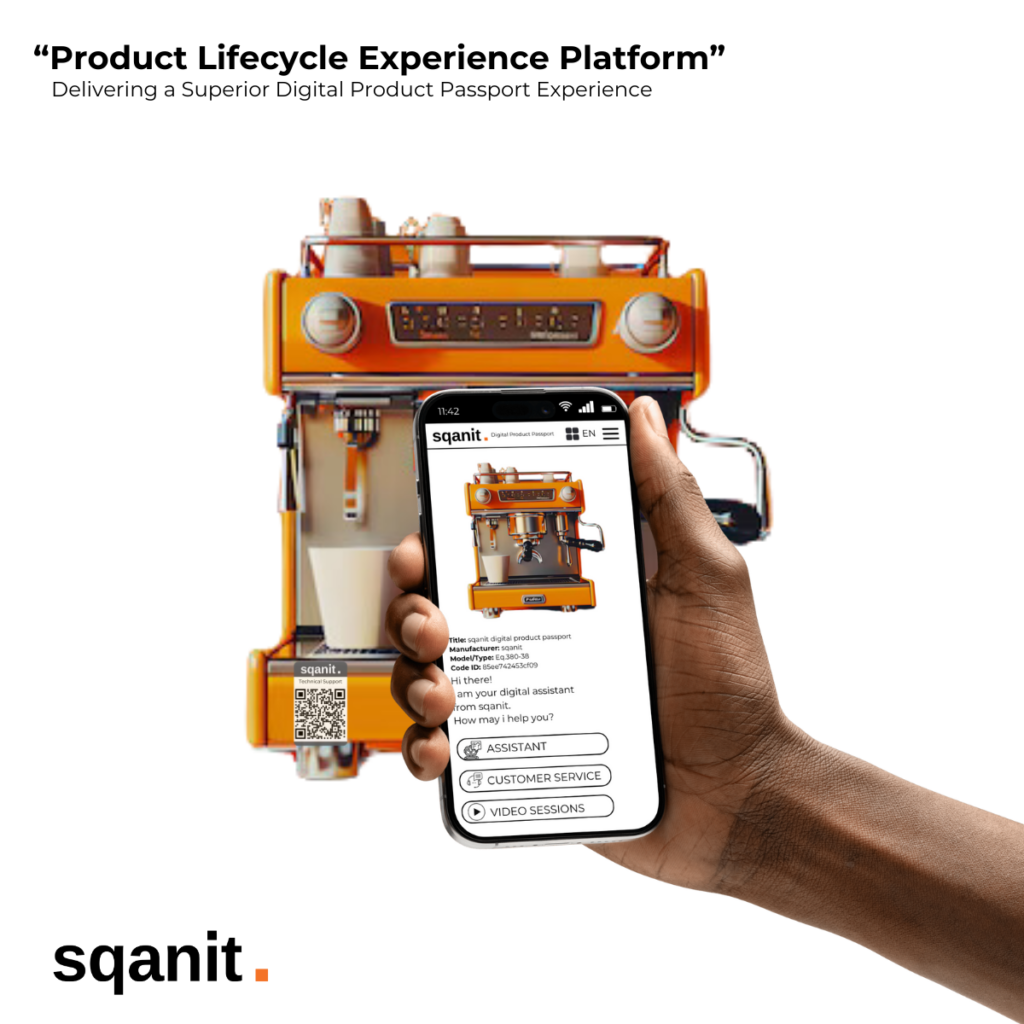
Digital Twin Application Areas
Digital twins find diverse applications across various industries. Key areas of use include:
Automotive and Aviation: Digital twins are utilized for performance evaluation, maintenance planning, and safety analysis of vehicles and aircraft, ensuring operational safety and reliability.
Manufacturing and Industry: In production facilities, digital twins are employed to monitor, analyze, and optimize machines and production processes, enhancing overall operational efficiency.
Healthcare Sector: By creating digital twins of patient data, healthcare providers can develop personalized treatment plans and optimize treatment processes for better patient outcomes.
Smart Cities and Buildings: Data analysis regarding energy consumption and water usage allows for the development of smart management systems for urban infrastructure and buildings, promoting sustainability and efficiency.
Relationship between Digital Twin and Digital Product Passport
Digital twin technology and the Digital Product Passport (DPP) are two innovative solutions that complement each other effectively. As we discussed earlier, a digital twin represents a real-time digital replica of a physical object, system, or process. In this context, the Digital Product Passport serves as a comprehensive repository of crucial information about a product.
Under the Ecodesign for Sustainable Products Regulation, it will soon be mandatory for every product to have a digital passport. These digital product passports will provide users with vital data, including the product’s environmental impact, the materials used, energy consumption, and recycling processes. This ensures a transparent flow of information about the product for consumers.
The digital twin plays a critical role in this ecosystem by continuously updating and monitoring this data in real time. As a result, the DPP can deliver accurate information to both users and manufacturers at every stage of the product lifecycle. This synergy not only enhances transparency but also fosters trust between manufacturers and consumers.
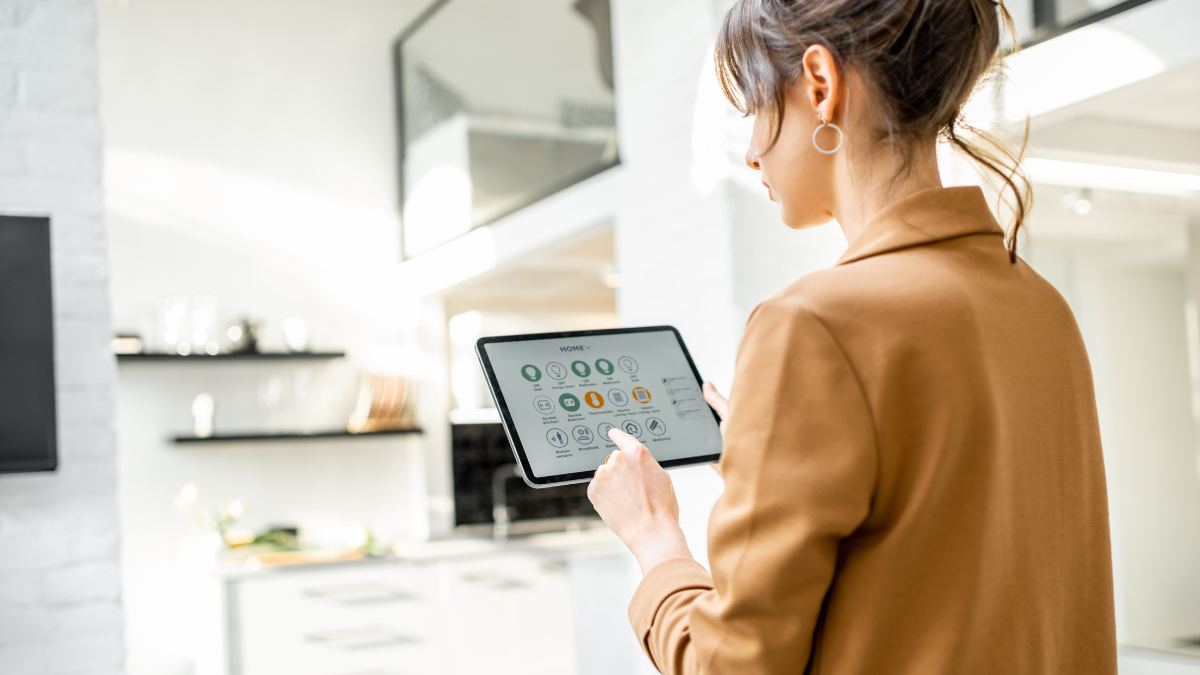
sqanit seamlessly integrates digital twin technology with its Product Lifecycle Experience (PLX) platform, providing manufacturers with access to comprehensive and up-to-date information about their products. As a key feature of the PLX platform, it offers an exceptional Digital Product Passport (DPP) experience for users.
This integration empowers companies and users to manage the entire product lifecycle—from production to usage and recycling—more efficiently. It also establishes a direct communication channel between users and manufacturers, ensuring ongoing engagement.
This capability is a significant advantage for companies aiming to achieve their sustainability goals and for brands seeking to provide transparent information to users, ultimately maximizing the total lifetime value of their products. With the help of digital twin technology, sqanit’s solution ensures that all data related to the product lifecycle is instantly accessible, enhancing compatibility with digital product passports.
Some of the opportunities that sqanit offers to users include:
- AI-Powered Self-Service Options: Enables users to quickly find answers to their questions.
- File Management: Simplifies the organization and storage of user manuals and other essential documents.
- Service Communication: Features chat and ticketing systems that provide users with instant support.
- Augmented Reality (AR) Supported Remote Assistance: Offers visual guidance to help users navigate and resolve complex issues.
Using the coffee machine example again, when users encounter problems, they can simply scan the QR code on their coffee machine. Within seconds, they can access all relevant information without spending hours trying to reach customer service. They can view the manuals and find solutions through pre-prepared questions and answers. For more significant issues, users can easily create a ticket and connect with customer service in minutes without needing to provide additional information. If the problem requires further investigation, they can schedule a video chat with a customer representative using Augmented Reality for more in-depth support.
With these solutions, brands not only comply with upcoming regulations and digital product obligations but also provide exceptional after-sales service to their users, helping them maximize the total lifetime value of their products.
For more information on regulations and the Digital Product Passport, check out our article, Digital Product Passport: A Comprehensive Guide.
Digital Twin Examples in Industry
MedTech
In the MedTech sector, digital twins can represent patient physiology and medical devices, offering valuable insights for personalized treatment plans. This technology enables remote monitoring of vital health data and simulates medical procedures, leading to safer and more effective care. With these capabilities, MedTech companies can optimize device performance, predict care needs, and ultimately improve patient outcomes.
LabTech
Within the LabTech sector, digital twins replicate laboratory equipment and processes, facilitating the monitoring and optimization of experiments. They can simulate various test conditions and predict equipment failures, reducing downtime and enhancing accuracy in research and diagnostic procedures. This results in increased efficiency in research workflows and a deeper understanding of equipment maintenance requirements.
Home Appliances
Digital twins for home appliances model devices such as refrigerators, washing machines, and HVAC systems, allowing manufacturers to monitor performance in real time. This capability helps predict maintenance needs and optimize energy consumption, thereby enhancing the user experience. By providing remote diagnostics and proactive support, digital twins contribute to extending the lifespan of devices and boosting customer satisfaction.
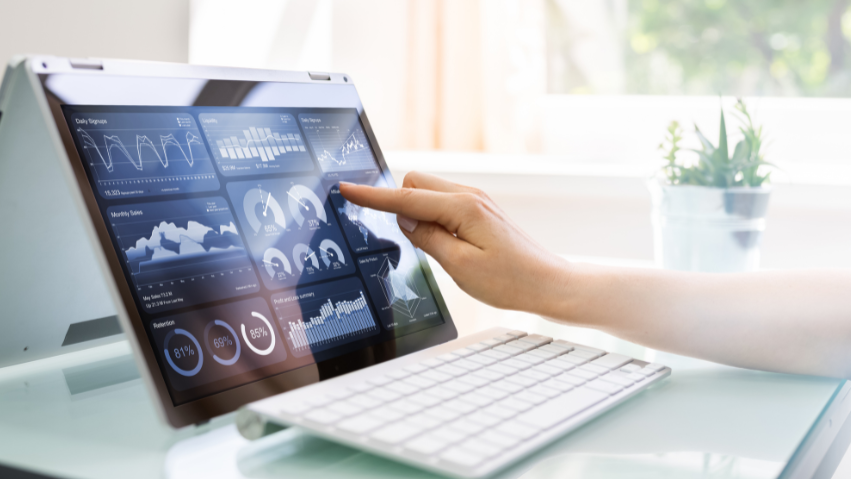
Industry 4.0 and Digital Twins
Industry 4.0 represents the fourth industrial revolution, characterized by the integration of digital technologies in industrial production. This revolution aims to enhance production processes by making them more efficient, flexible, and sustainable through automation, data exchange, and smart production systems. Digital twins play a crucial role in this transformation.
Digital Twins Role in Industry 4.0
Sustainability: By analyzing energy consumption and waste production, digital twins contribute to the development of more sustainable manufacturing methods, promoting environmental responsibility.
Increased Efficiency: Digital twins optimize the performance of machines and systems by simulating production processes, allowing for better decision-making and resource allocation.
Real-Time Monitoring: They enable continuous monitoring of physical assets, providing valuable insights into their status and performance.
Comprehensive Analytics: When combined with big data analytics, digital twins help users gain a deeper understanding of production processes, identifying areas for improvement and innovation.
Prototyping and Testing: Digital twins allow for the testing of designs before creating physical prototypes, streamlining the product development process and reducing time to market.
Conclusion
As a result, digital twin technology enhances the connection between the physical and digital worlds, allowing for more efficient management of processes and assets. By enabling real-time data tracking, facilitating simulations, and improving maintenance processes, digital twins hold significant potential across various industries. As technology continues to advance, the concept of digital twins will become increasingly prevalent and will play a vital role in the digital transformation processes of businesses.